Since its inception, Motomar has been one of the leading companies in the outfitting of the largest luxury yachts.

One of our main strengths lies in our organizational structure, combining industrial aspects in terms of operational methods and production processes with craftsmanship skills to meet the customization demands of each individual order. It is here that our dedication to work and meticulous attention to detail shine through our creations.
Our experience in design and manufacturing of innovative and customized products for mega yachts, enables us to optimize the operational phases, presenting new projects and transitioning to their realization in significantly shorter timeframes compared to less specialized companies. Furthermore, we can provide accompanying user manuals.
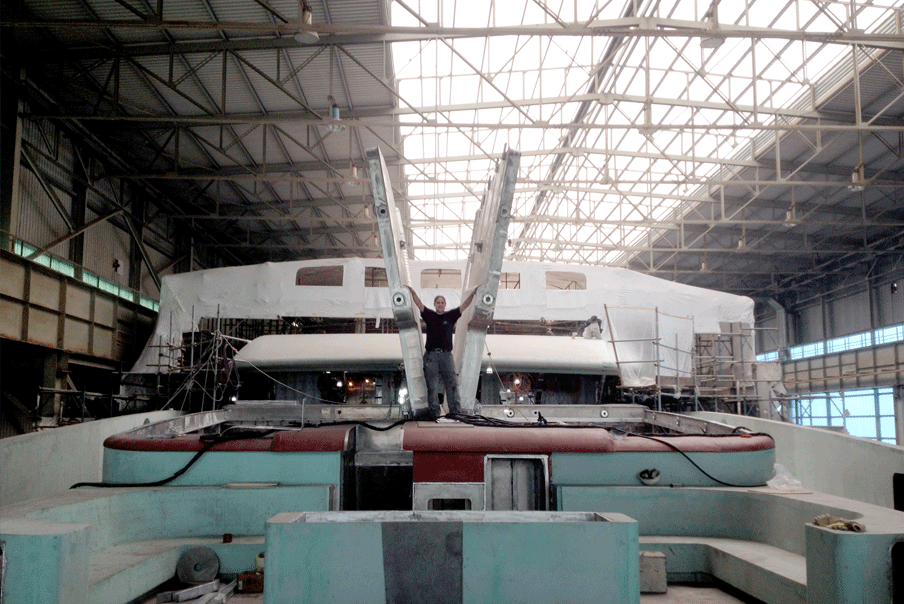
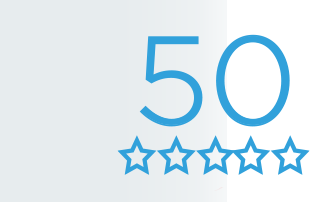
Experience
Extensive experience in the industry, accumulated over 50 years of history.
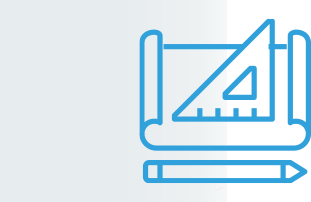
Internal Design
Internal design, including individual component design.
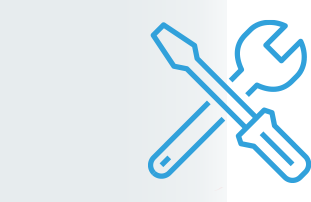
Internal Production
Internal production of all mechanical, hydraulic, and electrical components to ensure the availability of spare parts even years after completion.
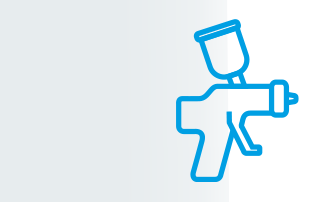
Internal Painting
An internal painting department to guarantee the necessary quality for products used at sea, ensuring the use of certified paints and consistent coloration.
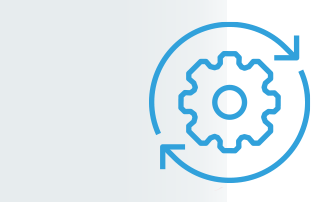
Installation Speed
Our products are designed to facilitate fast and easy onboard installation, allowing shipyards to maximize time and resource efficiency.
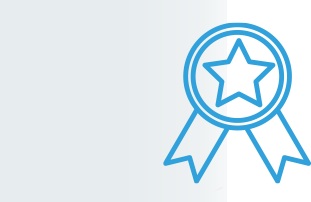
Product Quality
Constant experimentation with the latest technologies and new materials to consistently offer products with the highest levels of quality and reliability.
CONTACT US
Information request